图:锂离子快充影响因素
①热效应。对于单体电芯,快充条件下要承受电流增大导致的发热问题。在快充时,电池内外温差超过10摄氏度,热分布的不均匀与过高的温度将引发一系列问题:粘结剂解体、电解液分解、SEI钝化膜的损耗以及锂枝晶等。直接导致的危害有:电池循环寿命降低、热失控引发的安全问题。

图:快充导致电芯内外部温差>10℃
②锂析出效应。高充电倍率下,锂离子在负极嵌锂的过程变得不均匀,会因为无法及时嵌入负极石墨层而在负极表面沉积,逐渐形成锂枝晶。充电倍率越高,沉积的锂枝晶越多。锂枝晶的积累可能会刺破隔膜,造成电池内部短路而导致热失控。锂枝晶在生长过程中会不断消耗活性锂离子,过程不可逆转,导致电池容量降低,降低电池使用寿命。

图:不同倍率下,锂离子电池负极的锂枝晶SEM图,图a-d分别对应1C/2C/3C/4C倍率
③机械效应。锂离子在正负极间快速的脱嵌会造成电池内部极高的锂离子浓度梯度,导致活性颗粒间的应力错配。应力积累到一定值,会导致活性颗粒、导电剂、粘结剂以及集流体之间的缝隙增大,并造成活性颗粒的微裂纹增加,将显著增加电池内阻,降低电池的循环寿命。


在电池快速充电技术中,负极、电解液、粘结剂和隔膜是关键因素。电解液是传递离子的介质,优化其成分和浓度可提高充电速度和效率。粘结剂固定电极和电解液,改善性能可提高电池稳定性和充电速度。隔膜隔离正负极,防止短路,优化设计可提高安全性和充电性能。以下将全面讲解各电芯材料对快充性能的影响。

图:各电芯材料对快充性能影响一览图
4). 在快充条件下,石墨层的嵌锂电位将接近锂沉积的电位(前面所提的析锂效应),从而降低电池的性能。

造粒的工艺步骤是在一定的温度和压强下,将物料植入球磨机中进行球磨,并筛分。一次造粒的目的是减小负极颗粒的体积,二次造粒的目的是将小颗粒粘结成大颗粒。对于倍率性而言,负极颗粒越小,颗粒的比表面积就越大,锂离子迁移的通道就会增加,路径变短,更有利于锂离子的运动;而对于容量而言,负极颗粒越大,压实密度越高,活性颗粒的空间利用率增大,更有利于储锂。通过造粒制备的二次颗粒可兼顾大小颗粒的优点。


表:颗粒越小,压实密度越小,比表面积越大
P碳包覆打造更大石墨层间距和通道,抑制石墨层剥落
(3)无定形碳与电解液的相容性更好,可以有效防止大分子有机溶剂的共嵌入,抑制石墨层的剥落。
左图:不同碳包覆比例石墨的倍率 性能,高倍率下碳包覆含量高,倍率性能更强
右图:沥青涂覆石墨负极SEM兔:经过涂覆的颗粒表面 更粗糙 ,可以减少负极与电解液的直接 接触
P硅碳负极:提升安全性+能量密度
(3)硅基负极当前存在的问题:(1)硅与锂离子的结合方式是生成一系列的合金相,体积膨胀高达300%,对材料的稳定性产生巨大的影响,体积膨胀会产生高应力,进而在充放电循环中,反复的脱嵌锂离子会使硅颗粒出现粉化的现象,电化学循环性能迅速下降,容量也再快速衰减;(2)硅体积的变化还会导致SEI膜的反复生成,这不仅降低了库伦效率,同时也增大了阻抗延缓了锂离子的传输速率。
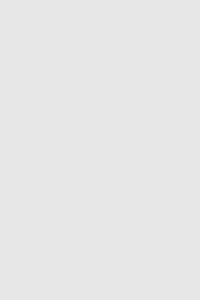
3、电解液
电解液影响负极结构稳定性及 SEI 膜等结构,调节电解液体系是提高电池快充性能的有效策略。在低浓电解液中,锂离子被大量溶剂溶解,形成锂离子溶剂化鞘层,在锂离子嵌入负极时易形成溶剂分子共嵌入,石墨层间微弱的范德华力难以在溶剂分子共嵌入后维持石墨片层结构;同时电解液中的添加剂和锂盐同锂离子形成 SEI膜,不同的添加剂及锂盐体系影响 SEI 膜的成膜,从而影响电池的循环寿命和倍率。因此调节电解液是提高电池快充性能的有效策略。
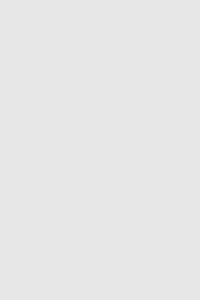
①溶剂的选择是影响去溶剂化动力学速率的关键因素:对石墨负极而言,在常规的低浓度电解液中,锂离子被大量溶剂溶解,形成锂离子溶剂化鞘层。当锂离子嵌入石墨阳极时,溶剂分子在石墨的夹层中发生共嵌入,随后的电解质分解导致石墨发生剥落。这是因为锂离子和溶剂分子之间的强配位作用使其很难去溶剂化,而石墨层间的微弱范德华力很难在溶剂分子共嵌入的条件下依然维持石墨的片层结构。因此,调节电解质的溶剂化结构,有效抑制溶剂分子共嵌入,是提高石墨的快充性能的一种有效策略。
溶剂化锂离子嵌入石墨之前,必须剥离其溶剂化鞘层。而这一过程的能垒较高(> 50 kJ∙mol−1),因此严重阻碍了石墨的快充性能,特别是在低温的条件下。因此,有必要对溶剂分子进行合理的调控,以降低石墨/电解质界面的去溶剂化能垒。溶剂化效应的本质是路易斯酸(锂离子)和路易斯碱(溶剂分子)之间的配位,因此溶剂的选择是影响去溶剂化动力学速率的关键因素。
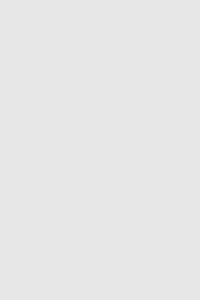
新型锂盐LiFSI被认为是在快速充电系统中增加导电性的一种有潜力的替代锂盐。在快速充电条件下,电解液对于离子电导率和热稳定性有更高的要求。与其他锂盐(LiFSI>LiPF6>LITFSI>LiCIO4 LiBF4)相比,在常规电解液中添加含LiFSI的电解液具有更高的电导率,并且含氟量更低,更环保。因此,在快速充电电池领域中,LiFSI被认为是最有潜力替代LiPF6的锂盐之一。
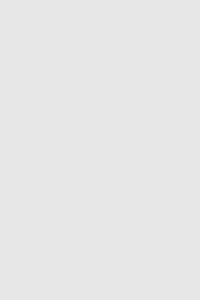
③部分功能性电解液添加剂也可以通过改变溶剂化结构来避免溶剂分子在石墨负极的共嵌入。研究人员对比了氟代乙酸酯(FEC)和碳酸亚乙烯酯(VC)添加剂对全电池体系中石墨负极大电流充放电时析锂情况的影响,发现适当含量 FEC 的加入有助于在石墨阳极上形成理想的 SEI 膜,从而有助与提升石墨的快充性能。
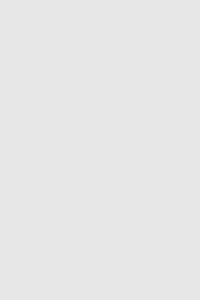
4、粘结剂
在电池中,粘结剂的作用是将电极材料粘合在一起。在快充过程中,粘结剂会受到电极材料和电解液之间的相互作用力,这些作用力会导致粘结剂的分解和电极材料的剥离。分解后的粘结剂会阻塞电极材料的孔隙,阻碍锂离子的传输,进而影响电池的充放电性能。因此,我们需要开发高强度、耐高温的粘结剂,以适应快充对电池的高要求。
锂电池粘结剂可以分为油性和水性两大类,其中油性粘结剂的典型代表是PVDF,而水性粘结剂则包括CMC+SBR和PAA等。
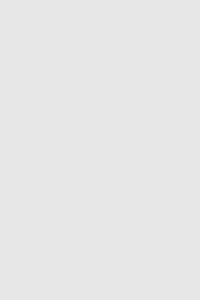
相比之下,CMC+SBR的黏附力有限,而新型粘结剂PAA则因其特殊性质在锂电池领域迎来了发展机遇。PAA具有以下优势:PAA具有较强的黏附力:PAA的侧链含有较多的基官能团,可以与负极活性物质表面形成氢键,从而有效地将负极活性物质与集流体连接在一起。 PAA可以形成类似于固体电解质界面(SEI)膜的包覆层:通过与硅形成类似SEI膜的包覆层,PAA能够改善硅基负极的循环性能,减轻其膨胀特性对电极结构的影响。
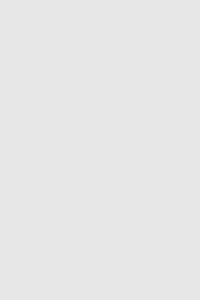
5、隔膜
在电池中,隔膜的作用是隔离正负极电极材料,防止短路的发生。隔膜的性能对于锂离子电池的许多方面都有影响,包括锂离子的扩散速度、电解液的保持性、系统内阻和电池界面结构的组成等,进而影响电池的容量、寿命和倍率性能等。在快充过程中,隔膜会受到电解液中离子迁移产生的应力作用。这些应力会导致隔膜的变形和破裂,破裂的隔膜会导致正负极短路的发生,进而影响电池的安全性能。同时隔膜的厚度、孔隙率和透气度对锂离子电池快充影响较大,电池提高快充特性优先选择更薄、孔隙率和透气度更高的隔膜。因此,我们需要开发具有高强度、耐高温、抗离子迁移能力的隔膜材料,以确保电池在快充过程中的安全性能。
快速充电对电池性能的要求推动了有机涂覆材料的需求增加。隔膜涂覆技术是一种应用于锂电池生产的技术,通过在隔膜表面涂布涂覆材料,全面提升隔膜的性能,特别是热稳定性,从而提高电池的安全性能。由于隔膜的主要原材料聚乙烯和聚丙烯的热变形温度较低,高温下会发生严重的热收缩,导致电池正负极接触而出现短路,可能引发火灾或爆炸。 涂覆技术可以使用不同类型的涂覆材料,其中包括无机材料和有机材料,以提高隔膜的热稳定性和综合性能。
无机材料如Al2O3(氧化铝)、勃姆石等是最常见的涂层材料类型,这些材料可以提高隔膜的耐高温性能,并具有良好的吸液和保液能力。它们可以降低热收缩率,有效提升循环性能和安全性能。例如,在聚乙烯基膜上涂覆了勃姆石后,热稳定性测试显示,当温度加热到170摄氏度时,涂覆膜几乎没有发生收缩,而隔膜已经发生明显形变。 有机材料:如PVDF(聚偏氟乙烯)、PET(聚酯薄膜)、纤维素、芳纶等。这些材料具有高粘结性和优异的吸液及保液能力,可以降低内阻,提高电化学性能。例如,通过在聚乙烯基膜上涂覆PVDF,可形成大量微孔结构,提高电解液的保持率。
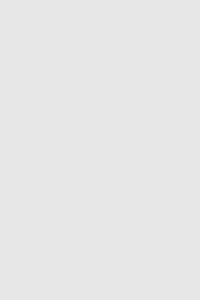
在快速充电系统中,相比无机涂覆材料,有机材料在孔径大小、电解液浸润性和稳定性等方面表现出明显的优势。聚烯烃隔膜具有较好的机械强度和电化学稳定性,均匀的孔结构以及适宜的热闭孔性能。然而,由于聚烯烃材料本身的疏液特性和低表面能,导致电解液的浸润性较差,同时在高温下会严重收缩。 聚烯烃隔膜的孔径大小约为100纳米x400纳米;PET和纤维素隔膜由直径为0.2-2微米的纤维交织堆叠而成;芳纶隔膜由直径为2-4微米的纤维交织堆叠而成,具有较大的孔径,可提供离子快速迁移的通道。此外,芳纶是一种极性材料,具有出色的耐温性能和较高的破膜温度,提高了电池的安全性能,并且与电解液有良好的浸润性,有利于电解液的吸收。因此,具有高电解液浸润性和吸液率的隔膜应用于锂离子电池能够提高电池的倍率性能和循环性能。
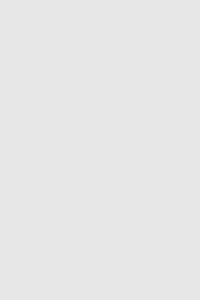
6、导电剂
导电剂是锂电池关键辅材之一,在活性物质之间、活性物质与集流体之间起到收集微电流的作用,以减小电极的接触电阻并加速电子的移动速率,也能有效提高锂离子在电极材料中的迁移速率,从而提高电极的充放电效率和倍率。
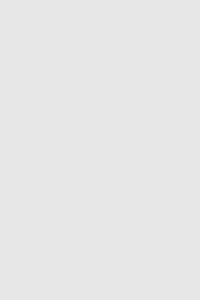
7、生产工艺
(1)浆料
(2)极片面密度
理论上来讲,倍率型电池与高容量电池不可兼得。正负极极片面密度较低时,可以增大锂离子的扩散速度,降低离子和电子迁移阻力。面密度越低,极片越薄,在充放电中锂离子不断的嵌入与脱出对极片结构造成的变化也越小。但是面密度过低的话,就会降低电池能量密度,成本升高,所以需要对面密度综合考虑。下图是个钴酸锂电池6C充电1C放电的例子,可以看看:
(3)极片涂布一致性
(4)极片压实密度
极片为什么要压实?一是提高电池比能量,二是提高电池性能。电极材料不同,最佳压实密度也不同。提高压实密度,电极极片的孔隙率越小,颗粒之间连接的越紧密,相同的面密度下极片的厚度越小,因此可减小锂离子的迁移路径。当压实密度过大时,电解液浸润效果不好,可能会破坏材料结构和导电剂分布,后期会出现卷绕问题。同样是钴酸锂电池6C充电1C放电,压实密度对放电比容量的影响如下图:
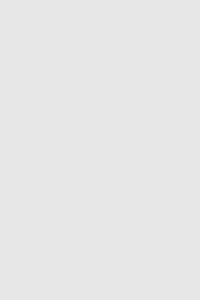
(5)化成老化及其它
8、结语