通过《ET7车身结构与涂胶连接》、《车身涂胶连接设计与规范》这2篇文章我们了解到了新能源车的车身结构与涂胶的质量要求。我们深刻的认识到,涂胶工艺是汽车白车身制造过程中非常重要的一环,随着汽车制造工艺水平的提高,车身涂胶的品种、 性能和工艺规范正不断的优化改进,涂胶设备也逐渐更新换代。
涂胶工艺不仅关系到车身的刚度、稳定性、抗腐蚀性能和声学性能,还直接影响整车的性能和外观质量。为了确保涂胶质量,焊装车间采用了多种质量控制方法,包括压覆检查、视觉在线监控以及涂胶控制流程等。在涂胶过程中,对涂胶外观质量、尺寸、连接性能等进行严格管理。通过开展涂胶过程质量管理,强化对涂胶人员工作技能、涂胶温度、涂胶工装、胶嘴直径、涂胶设备等精细化管理,确保白车身涂胶质量满足整车质量和性能要求。
白车身常见的引起涂胶质量问题包括但不限于:
钣金不平(如凸起、凹陷、变形、压痕等)、油污、锐边(毛刺、毛边等)、铁屑(焊渣)、痕迹(打磨痕、抛光痕、划痕)、白车身结构缝隙、焊缝密封胶外溢或脱落、锈蚀等。
这些质量问题不仅影响车身的外观质量,还可能影响到涂装的性能和耐久性。例如,钣金不平会导致涂层不均匀,影响美观和保护效果;油污和金属屑则可能导致涂层附着不良,影响涂层的耐腐蚀性。
新能源白车身的涂胶工艺过程控制对于提高整车质量和性能至关重要,需要通过对涂胶过程的精细化管理以及解决常见的质量问题来确保涂胶质量,今天,螺丝君就来重点介绍一下涂胶工艺的质量控制、常见质量问题及其解决方法。
一、涂胶工艺开发与验证
1、涂胶开发与验证工作一般分为以下五个步骤
涂胶后测量、夹紧后压合宽度测量、烘烤固化后整车状态确认、电泳拆解后测量、持续优化。
通过下表我们会持续了解结构胶、减震胶、折边胶、密封胶的对应工艺开发的五个步骤的具体要求:
1.1 结构胶&折边胶步骤及要求
1.2 减震胶&密封胶步骤及要求
1.3 测量方法示意
1.4 认证过程示例(结构胶&折边胶)
结构胶认证过程:
折边胶认证过程:
二、涂胶工艺质量控制
1、日常监控的要求
1.1 人工涂胶目视检查
人工工位通过目视检查是否漏胶、断胶、胶块、胶贴是否正确安装。
检查方法:
人工涂胶及胶块安装工位按照岗位操作指导书进行100%目视检查。目视检查只检查涂胶连续性(有/无)及大致位置,不进行定量测量。
1.2 自动涂胶检查
机器人涂胶工位采用远程摄像、拍照的方法进行100%检查(见下面示意图)。
1.3 物理测量检查
生产班组检查人工和自动涂胶是否符合工艺过程控制标准。
检查频次:
每班每车型1次,当班首车检查(除非条件不满足)。使用游标卡尺或直尺进行测量,并按照涂胶检查记录单,记录检查结果。任何涉及涂胶轨迹、参数或直径等相关调整后需要进行首台样本检查。
1.4 压合实验检查
① 通过压合试验验证得到符合产品质量要求的施工工艺标准,做压合验证前需要100%测量确保涂胶轨迹和涂胶宽度满足涂胶标准和相关控制公差要求;
② 日常生产每次涂胶工艺参数或轨迹变更的首件根据工程师判定是否需要做开合试验;
③ 压合验证无法实现的区域使用烘烤前破坏性检查或淋水进行补充验证;
④ 检查方法可参考涂胶工艺质量检查方法指导进行验证,使用游标卡尺或直尺进行测量,并将测量结果更新至检查记录单中。
2、涂胶破拆的要求
通过烘烤后电泳拆解车检查车身胶是否符合涂胶工艺认证标准。
检查频次:
参考质量拆解车计划,量产车型,一般单车型1台/月。
3、涂胶设备及参数控制
3.1 参数的建立与维护
车间工艺工程师在项目量产前2周,向设备集成商收集涂胶参数表,并将其完善至涂胶设备关键参数控制检查表中;并根据项目造车验证完成参数表的维护管理,在量产阶段将涂胶参数移交给区域设备工程师,后续由设备工程师完成参数的管理维护和传递。
3.2 参数的变更
车间工艺工程师和设备工程师以满足现场涂胶质量为依据,经过充分的验证后,可以对涂胶参数进行调整和变更,参数变更后需要对首台车进行全胶路的涂胶质量验证,参数变更后需要更新涂胶设备关键参数控制表。
4、涂胶视觉监控及要求
4.1 视觉技术在涂胶检测中的应用
涂胶作为白车身制造过程中的一种重要连接工艺,具有机械连接(如铆接等)、固态连接(点焊、摩擦焊等)不可替代的优势:
① 可以有效连接金属与非金属;
② 不会产生机械连接的应力集中问题;
③ 密封胶还可以起到密封作用,因此涂胶质量的控制就显得尤为重要。
常见的涂胶质量问题主要是位置偏差、物料量超差、断胶等。传统检测方式是采用人工抽检,缺点是操作性差、样本量少,有缺陷流出风险。
涂胶视觉检测基本原理:
涂胶视觉传感器(见下图)由光源和相机构成,实时拍摄2D图片,其内容包括胶枪嘴,以及底板阴影、胶条、胶条的反光。通过控制器进行示教得到胶条的骨架点,并设置区段检测参数。
最后,软件算法调用不同区段的骨架点和检测参数,将结果反馈至控制器,从而判断涂胶宽度、涂胶位置以及涂胶连续性是否符合设定质量目标。
视觉技术应用在白车身制造过程中,可将涂胶传感器集成在涂胶枪嘴上,如下图所示。工艺人员对胶条参数进行示教,实际生产过程中涂胶检测设备实时对涂胶质量进行监控,每个工件的涂胶检测结果以及回放可以在控制器中查看。胶条的位置、物料量超差或者出现断胶等控制失效情况时,控制器会报警,并在控制器中显示警告项的失效类型、超差量,工艺和维修人员可以据此追溯问题的真正原因。
在白车身制造过程中,涂胶过程的质量控制对于整车的强度、密封性和面品质量起着至关重要的作用。实际生产过程中,对于涂胶质量的检测手段一般采用对关键位置进行人工测量。视觉技术的应用不仅能检测关键帧,而且能做到实时全过程覆盖,不占用生产线节拍,从而可有效提高生产线的自动化率、质量控制等级和数字化监控。
4.2 涂胶检测系统硬件配置(见下表)
4.3 涂胶检测系统的工作原理(参考2.1.2中图示)
第一步:
用LED光源/激光均匀照射被测工件,获取胶条特征;
第二步:
三个相机360°无死角拍摄,获得完整、连续的胶条图像信息;
第三步:
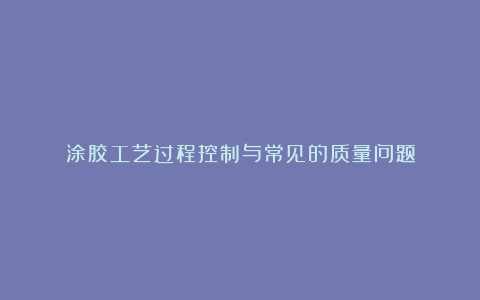
通过图像处理方式计算获得胶条的位置信息以及灰度信息;
第四步:
利用视觉信息判断待检测胶条的连续性、胶宽、位置、高度。
4.4 涂胶检测系统技术要求
1)涂胶检测系统采用独立的系统,不占用机器人和PLC的CPU运算资源;
2)存储机器配置双硬盘,并进行阵列配置,具备任何一个硬盘损坏不影响正常工作的功能,每个硬盘容量不小于2T;
3)系统需具备数据采集的功能,系统需支持不同厂商数据的读取,即其他系统可以读取拍照系统的数据进行监控;
4)系统软件需具有中文和英文两种语言可选;
5)系统控制柜的需配置扇热风扇或空调;
6)涂胶检测需能检测胶条的连续性、宽度、位置度,如需要检测胶条高度,则在设备选型时选择具备检测高度集成相机和软件;
7)检测的精度需达到连续性±0.5mm、宽度±0.1m、位置度:±0.1m、高度±0.15mm;
8)涂胶检测为实时检测,没有额外的生产节拍;
9)集成相机需具备颜色兼容性,能检测各种颜色的胶条;
10)集成相机为内部集成光源,不需要额外配置光源;
11)涂胶的速度需满足最高600mm/s的要求;
12)工作检测距离需覆盖85mm-230mm的范围;
13)集成相机对胶条需360°全覆盖,保证100%的涂胶检测。
三、涂胶常见的缺陷和控制
溢胶:
溢胶的直接后果首先是返工。如果未清除溢出的胶料,不仅会污染制造工具,还会污染电泳池,进而引发其他的问题。当折边零部件到达油漆车间时,溢胶会导致设备密封件出现问题。
产生原因:
涂敷太多胶料:在包边过程中,多余的胶料会溢出。
机器人调试(胶条位置)不准确:如果胶条位置不正确,则会严重影响折边内部的胶料分布。如果未按照要求填充折边区域内的间隙,也可能导致溢胶。
控制手段:
调整设备参数,实现胶料精准控制,对于涂胶轨迹监控,异常情况报警,后进行调整。
曲流:
这种现象描述了自然界可见的一种图案。曲流是对河流的描述,它有额外的河流环路并形成弯曲的图案。这种图案也可见于折边涂胶,但仅在固化后打开部件时才能看见。
产生原因:
金属板的回弹行为:在包边后,两块金属板位于折边位置之外。在弹性行为的作用下,它们通常会略微分开,这可能导致折边内的胶料分布不均匀。
零部件过度冲压:每种折边方法都各有利弊。在折边工艺中施加的作用力可能导致部分区域的胶料错位。
零部件的油污:当金属板离开冲压车间,或从缓冲库存到货架时,其表面通常为含油状态。油可能会妨碍胶料实现最佳分布效果,可导致部分区域的胶料错位。
控制手段:
控制车身钣金与零件质量、保证车身钣金与零件的清洁度。
PVC气泡:
如果折边密封件将空气封闭于其中,则可能导致在后续工艺步骤后出现肉眼可见的问题。当车身通过烘炉时,由于折边区域和密封内部水分蒸发,因而会产生所谓的PVC气泡(见下图)。PVC气泡会影响车辆的美观,因此,汽车制造商都竭力避免出现这些气泡。
产生原因:
气泡已经包含在胶料内,并在应用期间涂敷。
在应用工艺期间或之后形成气泡。在包边或电泳涂装期间,气泡也可能会进入折边区域内。
控制手段:
优化填充工艺,实现要求区域100%填充,优化包边前缘间隙,胶嘴切入角度及涂胶手法。
单面粘接:
胶水只粘结在了单侧零件上
发生原因:
钣金间隙较大或者钣金表面油污或其他污染
控制手段:
清洁钣金表面,保证钣金表面清洁度,优化钣金间隙。
胶未压开:
胶水未达到压合宽度要求
发生原因:
涂胶参数问题或者钣金间隙问题
控制手段:
优化涂胶参数、优化钣金间隙。
网状粘胶(胶水回弹):
胶水压开后零件回弹,导致的弱连接。
发生原因:
涂胶参数问题或者钣金间隙问题
控制手段:
优化涂胶参数、优化钣金间隙。
螺丝君经验与总结
L.S.ENGINEER Experience and Summary
以上就是螺丝君对涂胶工艺过程控制与常见的质量问题粗略的讲解,对于典型的问题,只是简单进行一些说明和介绍,每个问题点的控制都是一个值得研究的课题,随着新能源汽车对车身结构轻量化设计的要求,对于车身的密封、刚性、强度等方面都提出了严苛的要求。
所以在生产制造端,对于每个问题的过程细节控制就尤为重要。后续章节螺丝君会再选1~2个问题点进行详细的研究与介绍,也欢迎大家与我们一起探讨和学习。
#artContent h1{font-size:16px;font-weight: 400;}#artContent p img{float:none !important;}#artContent table{width:100% !important;}