发布日期: 2024/10/23
用等离子使金属粒子呈圆形-高效生成适合层叠造型的金属粉末-
重点
开发高效生成球状粒子的等离子加工技术
通过使金属粒子呈球状且形状均匀来提高填充密度,实现高品质的造型物的形成
可以无浪费地使用各种形状的粉末,为低成本化做出贡献
概要图
概要
国立研究开发法人产业技术综合研究所(以下称为“产总研”)制造技术研究部门板垣宏知主任研究员开发出了通过控制气流和压力,将由等离子加热的金属粒子加工成正球状的技术。
在以金属为对象的3D打印技术——金属层叠造型中,主要使用粒径为10~150 µm的金属粉末。 要制作高质量的产品,需要使用作为造型材料的粉末的形状接近圆球、粒径分布和形状均匀且缺陷少的金属粉末。 另外,在粉末粒子间含有大量间隙的低填充密度粉末中,会在成型物中引起空隙和龟裂等内部缺陷,这将导致产品的质量下降和可靠性问题。
在本研究中,利用在等离子体加热处理中用于控制气体分子运动的压力控制,开发了有效分离粒径接近圆球形状的金属粒子和作为副产物产生的粒径1 m以下的微细粒子的装置,成功地制作了即使在松散的填充方法中也能够提高填充密度的金属粉末。 本技术可以将各种形状的金属粉末加工成适合层叠造型的粒子。 也可以利用廉价的材料和使用过的粉末,以低成本制作高品质的产品。
这个开发品将在2024年10月29日开始举办的高功能素材Week的展位(可持续材料展39-25 )上展示。
开发的社会背景
金属层叠造型的施工方法与以往的铸造和锻造等施工方法相比,可以实现金属部件的轻量化和高功能化,支持定制,缩短制造时间。 特别是在航空宇宙等领域,具有缩短使用难以加工的材料的零件的制造时间和通过一体制造可以轻量化的优点,正在研究在各种零件上应用层叠造型。 另外,使用金属和树脂等各种材料的积层造型技术正在被开发,从2011年到2021年,金属积层造型装置的世界累计普及台数增加到了约1.4倍( Wohlers Report 2022年)。 并且,预计到2030年年均增长率将达到23.9% (美国Grand View Research(2022年2月) ),金属层压技术作为新的制造技术备受期待。
在金属层叠造型中,主要使用粒径10〜150 µm的微小金属粉末。 该工艺的稳定性和造型物的质量受粉末特性的强烈影响,因此粉末的特性和质量的提高对于制作高质量的造型物非常重要。 金属粉末中含有的气泡和间隙、金属粉末的填充密度的降低会成为造型物内的空隙和龟裂等内部缺陷的原因。 因此,作为造型材料的粉末材料要求是粒径分布均匀、形状也接近圆球、气泡和间隙也少的能够高填充密度的金属粉末。 许多金属粉末为了达到高质量标准,采用气雾化法制备,但制备成本高,可用材料种类也有限。 因此,希望开发出以高生产率制造适于层叠造型的金属粉末的方法。
研究的经过
产综合研究所为了增加可用于金属层叠造型的材料种类,实现廉价且生产性高的粉末制造技术,正在进行利用等离子加热,由非球状的金属粉末制造高真球且均匀形状的粒子的研究开发。 水雾化法制成的粉末和破碎粉末是不适合层叠造型的非球状。 考虑到如果使用直流电弧等离子体对其进行加工,实现圆球度高的粉末,层叠造型过程所需的粉末的流动性和填充性就会提高,从而能够制作高品质的造型物,因此致力于开发。 并且,通过利用压力使气体原子或等离子粒子的平均自由工序变化,能够选择性地分级次要产生的1 m以下的微细粒子,并且通过利用等离子体,也能够期待等离子体中的离子、电子、活性种引起的粉体表面的润湿性的提高和杂质除去的效果
研究内容
使用直流电弧等离子体将金属粉体加热到熔点以上的高温时,会产生金属粉体的熔融和气化,因此熔融的控制很重要。 在加热过程中,粉体粒子的表面被加热,其热量传递到内部,最终粉体粒子熔化形成球形粒子。 在这个过程中,粉体粒子的表面和内部会产生温度差。 因为表面附近超过金属的沸点,所以金属会气化。 该气化的金属可能再次凝固,形成粒径1 m以下的微细粒子,附着在加工过的金属粉体上。 由此,球度和流动性降低,表面杂质增加。 为了提高粉体粒子的球化效率,提高等离子体的温度(输入功率)是有效的,但这样会导致粉体粒子表面和内部的温度差变大,金属的蒸发量增加。 其结果,再凝固的微细粒子增加,附着在球状粉体粒子上的微细粒子的数量也增多,使填充密度和流动性恶化。
为了解决这一问题,开发了通过控制气流和压力来管理金属粉体的蒸发和再凝固,只去除粒径1 m以下的微细粒子的等离子加工技术。 由此,可以在微细粒子附着在加工后的金属粉体上之前,有效地将其去除。
图1开发的装置的照片和等离子加工流程概略
图1概述了所开发设备的照片和流程。 在此过程中,可以通过控制压力来调节气体分子的平均自由程。 粉体粒子的粒径小于平均自由行程时,流体阻力呈指数函数减少。 根据坎宁安修正系数( Cc ),常压时粒径1 m附近Cc开始大于1,因此粒径1 m以下时气体原子的平均自由行程的影响无法忽视,流体阻力开始降低。 越是低压,越能增大流体阻力开始下降的粒径。 由于金属层叠造型中使用的粉末粒径为10〜150 µm,因此通过控制气体分子的平均自由行程,可以减少并有效去除几微米以下的微细粒子的流体阻力。 本研究控制气流,以在附着于金属粉体粒子之前除去从金属粉体的蒸发中再凝固的微细粒子。 由此,调整工艺压力,使微细粒子在电弧等离子体加热源附近的排出效率变高,设计了产生去除气流的装置。 结果,用于积层造型的直径10〜70 µm的粒子和直径1 m以下的微细粒子成功分离。
图2等离子体处理前后金属粉末形状
图2显示了用扫描型电子显微镜观察等离子体处理前后的金属粉体粒子的照片。 从这张照片中可以看出,等离子处理后球状的金属粉体粒子在增加。 等离子体处理后,圆度为95%以上的球状粒子的比例比处理前增加了约5倍。 另外,通过增加球状粒子的数量,使粉末流动所需的能量减少到约一半,成功提高了流动特性(图3 )。
图3等离子体处理前后球状粒子数的比例和流动能量的变化
图4显示了用扫描型电子显微镜观察了一般的等离子体处理后的金属粉体粒子和使用开发的技术制作的金属粉体粒子的照片。 如果放大观察用一般的方法进行了等离子体处理的金属粉体粒子,可以确认在其表面附着了很多微细粒子(图4(a ) )。 另一方面,在使用气流控制和流体的平均自由行程(压力)的控制技术的工艺中,通过利用由粒径引起的流体阻力的差异,得到了表面没有微细粒子附着的球状金属粉体粒子。 (图4(b ) )。
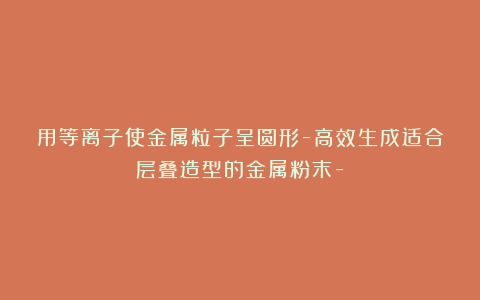
图4 (a )用一般方法及( b )开发技术制作的金属粉末
图5 (左)是以未处理的金属粉末(造粒粉末)和等离子处理的金属粉末(造粒粉末)为材料,用粉末床熔融结合( PBF: Powder Bed Fusion )型造型装置制作的积层造型物的照片。 以等离子处理的金属粉末为材料进行造型时,其造型面可以看到金属光泽,表面粗糙度(算术平均粗糙度)得到了改善。 这可能是由于等离子体处理提高了金属粉末的填充密度,金属粉末之间的间隙变少,从而抑制了熔融凝固时的体积减少。
图5通过pbf型积层造型装置造型的各粉末的造型物
今后的计划
为了即使使用非球状的金属粉末也能实现高质量的层叠造型,进一步推进有效的等离子工艺和造型工艺的构筑。 另外,作为用于层叠造型且质量下降的金属粉末的特性再生技术(再利用技术),通过包括金属粉末的再利用性在内的层叠造型进行评价。 我们希望通过降低金属粉末制造工艺的成本,推进能为金属积层造型技术的市场普及做出贡献的产官合作活动。
用语解说
等离子体
气体变成高温,气体分子和气体原子电离,由此带正电荷的离子、电子以及中性粒子共存,是电中性状态的集体气体。 也称为电离气体。
金属层压造型
以金属为对象的3D打印技术。 根据对象产品、零部件的3D形状的数据模型制作切片数据,一边熔化金属材料并凝固一边逐层堆积制作立体形状的加工技术。 金属材料一般使用粉末和电线,用于溶解这些材料的热源有激光、电子束、等离子等。
填充密度
用一定方法填充到具有一定容积的容器中时的粉体重量除以填充容器的容积得到的值。 该容积的值中也包括粒子间的空隙,粒子间的空隙越多,该值越小。
气体雾化法
在惰性气体气氛中或大气中通过高频感应加热等加热溶解金属试样,喷射高压惰性气体对金属粉末进行制粉的方法。 得到接近球形形状的粉末。 但是,微粉末有时会附着在更大的粒子上,或者由于高压气体卷入粉体内而在粉体内部产生空孔。
水雾化法
与气体雾化法不同,是向熔融的金属喷洒高压水来制粉金属粉末的方法。 生产率比气体雾化法高,但粉体形状为非球状,通过与水的反应,金属粉末的氧含量高。 因此,一般不用于金属层压造型。
直流电弧等离子体
热等离子体的一种。 向电极间施加高电压,通过电极提供的热电子和二次电子,维持由气体的绝缘破坏引起的放电。 放电中心的温度达到数千度以上,也适用于焊接和放电加工等加工技术和电炉作为热源。
坎宁安校正系数
在气体中运动的粒子从气体中受到的流体阻力的修正系数。 粒径达到与气体分子、或者气体原子不与其他分子等碰撞而移动的平均距离相同程度以下时,与将气体视为连续体的情况相比,粒子的流体阻力变小。 修正该流体阻力减少部分的系数是坎宁安修正系数。